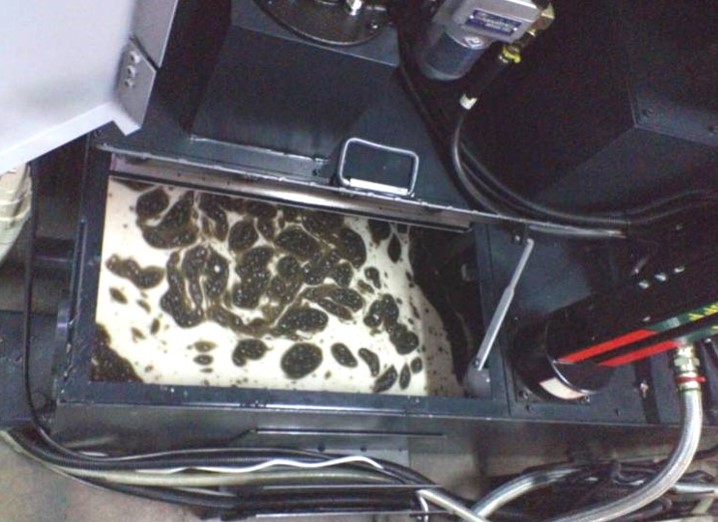
クーラント(切削液)の管理
水溶性切削液は切削加工に欠かせません。
しかし、管理を怠ると腐敗し悪臭を発するだけでなく、製品の加工不良につながる恐れもあります。
切削液の性能維持のため、日常的に液状態の確認、濃度管理を行いましょう。
-良い状態での使用開始
機械が汚れていると、張り込んだ新しい液がスラッジや雑菌に汚染されてしまいます。
切削液を補充する際は、タンク内の清掃を行ってから新しい切削液を張り込んでください。
-適切な使用方法(希釈、補充)
水➡原液の順で希釈を行います。
原液投入後はよく撹拌させ、タンクの規定量まで補充する。
※間違った手順(原液➡水)で希釈した場合、逆エマルジョンが生成されやすく、切削液がゲル化し溶解困難になります。
※水のみの補充はNG!
水だけを補充した場合、添加剤が補充されないため切削液内の添加剤量が減少し、錆や腐敗の原因となります。
水溶性切削液85-97%が水で構成されているため、希釈水の水質にも注目しましょう。
例えば、硬度が高い(硬水)と泡立ちにくく、硬度が低い(軟水)と泡立ちやすくなります。
泡が立ちやすい、消えにくいことでオーバーフローにつながります。
硬度が高すぎる場合、エマルジョン、ソリュブルの分離を引き起こす可能性があります。
また、切削油剤の影響を受けやすく、白濁や浮上物、浮上油等の要因となり得ます。
※水溶性切削液を希釈する際は、希釈装置の使用を推奨します。
<希釈装置を使用するメリット>
・濃度が安定する。
・エマルジョン粒子が細かく一定になる。
粒子が粗く一定でない場合、ワークや機械のべたつき、フィルタの詰り、濃度のバラツキの原因になります。
-液状態の定期的な確認
水溶性切削液の濃度管理は最も重要な作業です。
測定時はクーラント供給ノズルから出てくる液を測定してください。
(タンク液面の液を測定した場合、浮上油の影響を受けやすい為)
『 濃度=濃度計での読み×製品の換算係数 』
適正な濃度:5~15% 適正なpH値:8.0~9.4
<濃度が高い場合>
・発泡、べとつき、原液使用量が多い
<濃度が低い場合>
・加工性能の不足、防錆効果の低下、安定性の低下、pH値の低下、悪臭の発生
<pH値が低い場合>
・鉄系材質の腐食、安定性の低下、悪臭
<pH値が低い場合>
・非鉄金属の腐食、皮膚障害、発泡
-浮上油の除去
浮上油の除去を怠ると、これらがタンクの表面を覆い空気を遮断してしまいます。
その結果、タンク内で嫌気性の細菌が増殖し、切削液の腐敗が進みます。
切削液の腐敗は悪臭を発生させるだけでなく、油剤成分の種室による所性能の低下、配管・フィルタの目詰まりを引き起こします。
定期的に浮上油を除去し、切削液の腐敗防止に努めましょう。
-切りくず、スラッジの除去
定期的なクーラントタンクの清掃を行い、タンク内に堆積したスラッジを除去しましょう。
清掃を怠るとタンク内でスラッジが凝固・固着してしまい、除去が難しくなってしまいます。
<障害事例>
・切削液の吐出不良、ポンプ故障
・切削能力の低下、刃物の折損
・電食によるタンクの穴あき